
CASTING DEPARTMENT
Department that is responsible for the production of parts from the Waxing Department which work with dangerous machines, heat and chemicals. Those in this department must have a certain level of casting skills and have a high level of prudence. Each sub job card specifies the type of metal used for melting, such as silver, gold and platinum. The production process can be described as follows:
​
-
Pouring plaster: The workers use a plaster cement material that will be mixed with water (1 gram of cement / 38 g of water) through a mixing vacuum machine to make the bubbles disappear by mixing in 8 minutes. Then pour it into the wax crucible.
-
Oven: The workers bring the wax crucibles to the oven to make the cement of materials trees to coagulate(20-30 cylinders of materials trees) about 1 hours. Then it will be brought into the cool oven to cool down so that the heat temperature of the cement decreases. After that, it will become the final print for casting process. The crucible is a cylindrical shape which made of steel or may be a better material than stainless steel. Which will be placed in the exact location and suitable for the base which was made for supporting the surrounding wax crucible. In the process of pouring the plaster cement into this crucible, the cement is carefully poured into the crucible and does not affect the wax, each crucible that has been poured down will be placed under a vacuum chimney where the vacuum will be released from the vacuum pump.
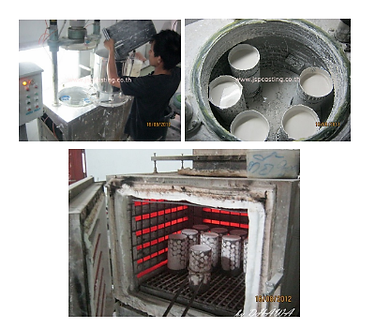
2.1 After the vacuum process, the baking process will eliminate the wax inside the cement by heating the crucible. On the crucible there will be a hole attached to each sample, which will be the hole for the outflow of wax that dissolves out and at the same time, it will be a channel for the molten any metal to enter the cavity of the mold in the casting process.

3.Casting process: There are 2 types of machinery for casting include centrifugal casting machine and vacuum casting machine. Centrifugal casting machine uses rotary motion to use force to push the molten metal into the mold. Vacuum casting machine uses vacuum and gravity to attract metal into the cavity in the mold (the factory uses the vacuum casting machine primarily). Vacuum casting machine process, the crucible will be moved from the furnace and placed in the mold with the top opening. The metal will be dissolved in the crucible and then flowed into the mold that is opened. At the same time, the vacuum system began to work, which would pump air out of the mold and suck the molten metal back into the cavity of the mold. This process takes about 12-15 minutes, depending on the type of metal used in the melting.

4.Cleaning process: The plaster will be cool down by placing the crucible in a cold water tank, including water spraying. Then the technician will clean it with Hydrofluoric acid and Nitric substance to clear the oxide or any objects that are stick into the cement for 5-10 minutes.

5. Sprue cutting process: The workpieces will be cut from the tree or its base and also cutting the metal prototype that is still left on the workpieces by using the grinding stone polishing wheel.
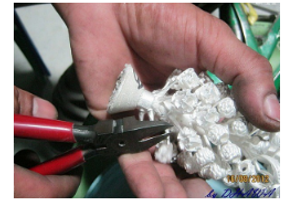
6. Polishing process: After the sprue cutting process, all workpieces will be put into the magnetic machine to polish the workpieces surface to make it is flat surface. This process will take time for 30 minutes and then rest to dry.
​
7. Inspection Process: The technician will check the quality of the workpieces according to the requirements in the quality of the casting piece. If the quality is fail, the workers will bring these workpieces to refine.
​
8. Casting Stock: After completing the above processes, all components will be sent to the Casting Stock to wait to be produced according to the order in the next process in the Post production department follow the Sub Job Card.
